混打綿〜梳綿〜練条 |
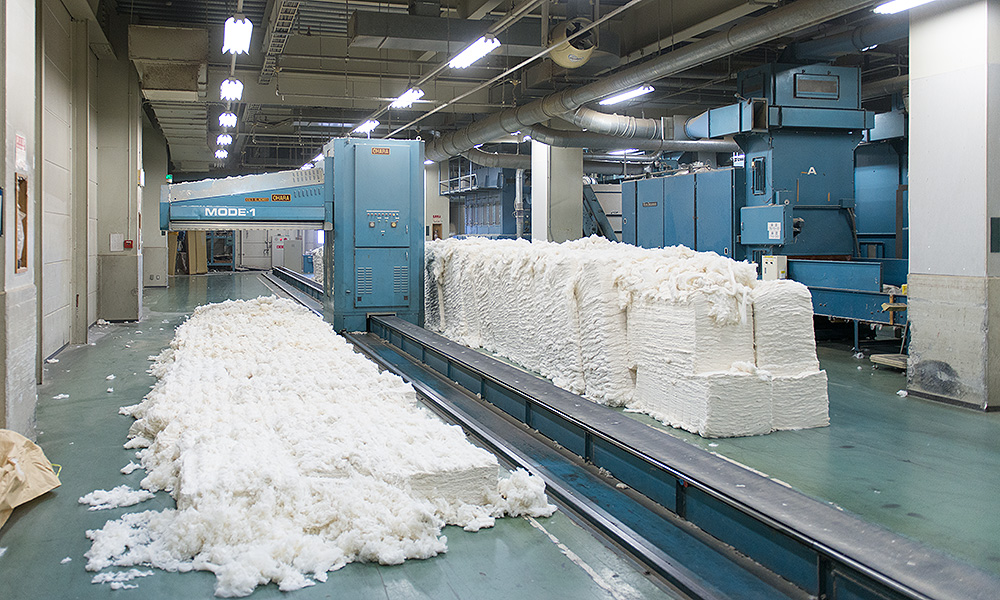 |
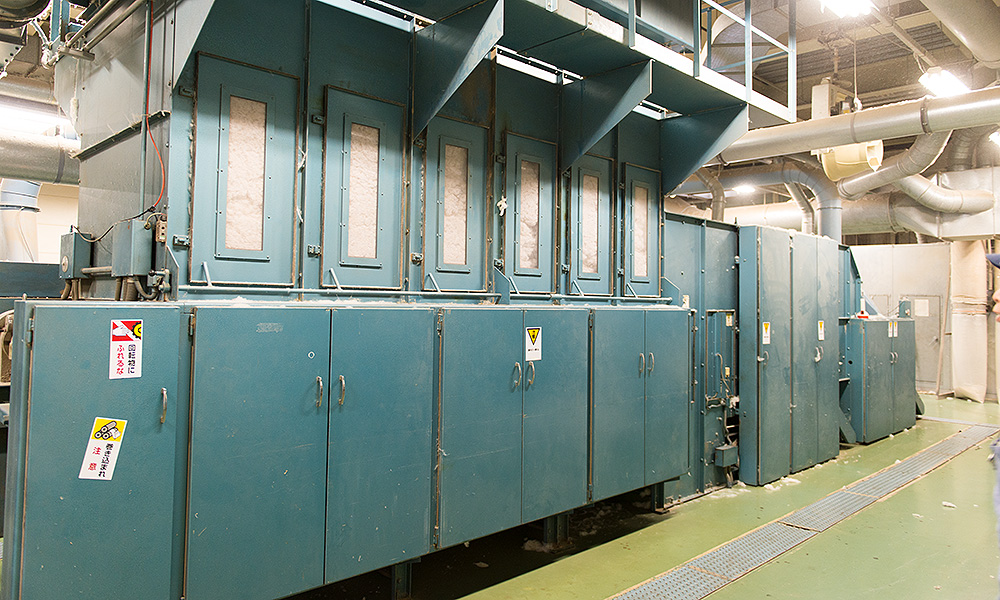 |
糸のムラ形状も決まりいよいよ量産紡績が始まる。まずは「開俵」。圧縮されパッキンに詰められた綿を開く。その後、適度な温度・湿度に保たれた部屋で一昼夜程度置くと固く引き締まった綿が緩んでくる。これにより、後の工程で葉カスを取り除いたり、ヨリをかけたり がしやすくなる。右は綿を空気で上に巻きあげ落とす事を何回も繰り返している。ジンで取り切れなかった葉カスや枝など、汚れをできる限り取り去る。 |
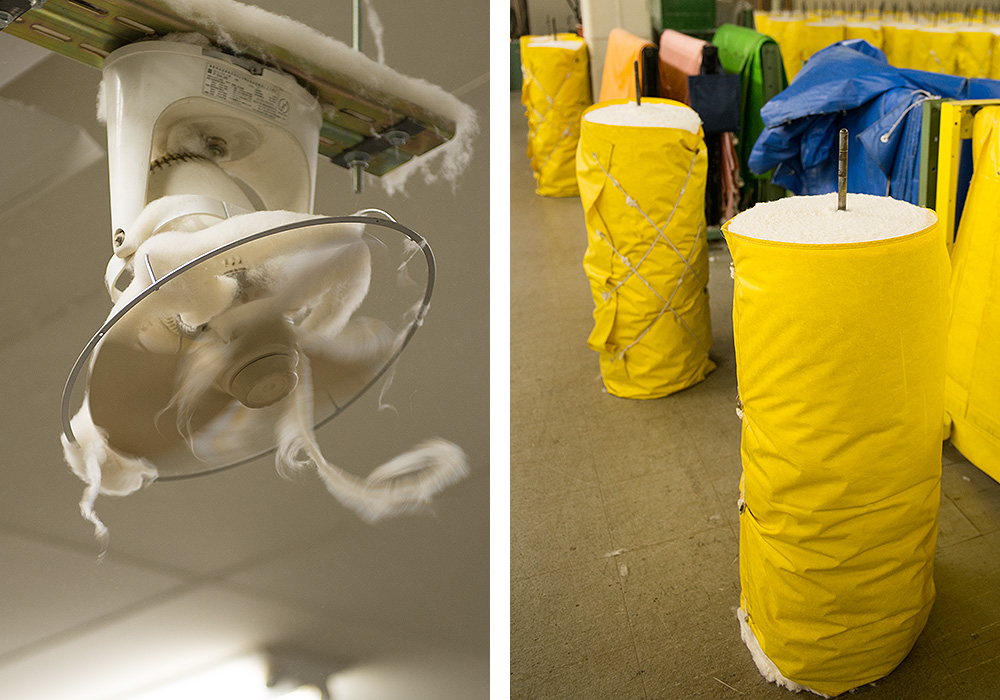 |
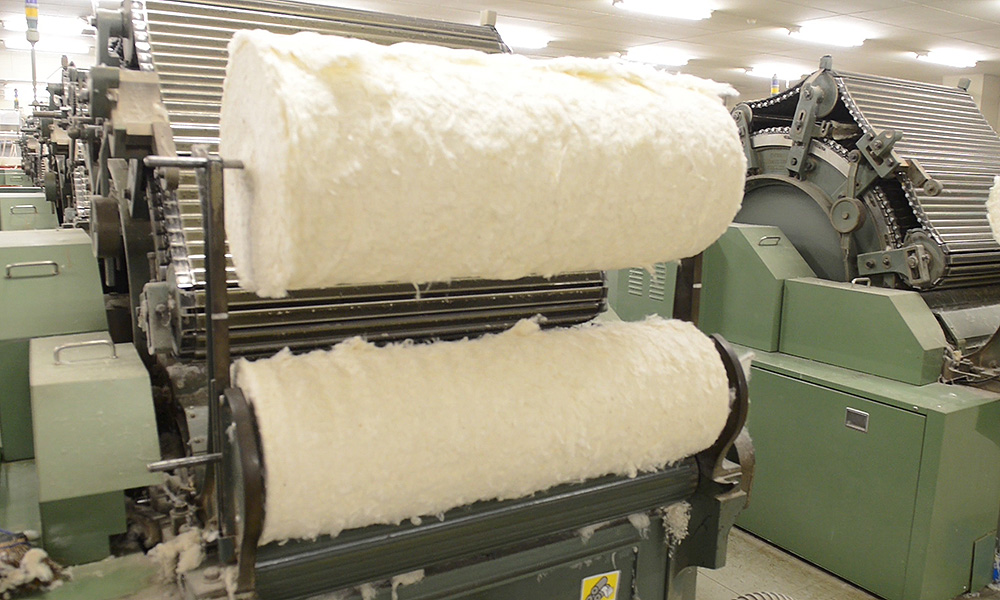 |
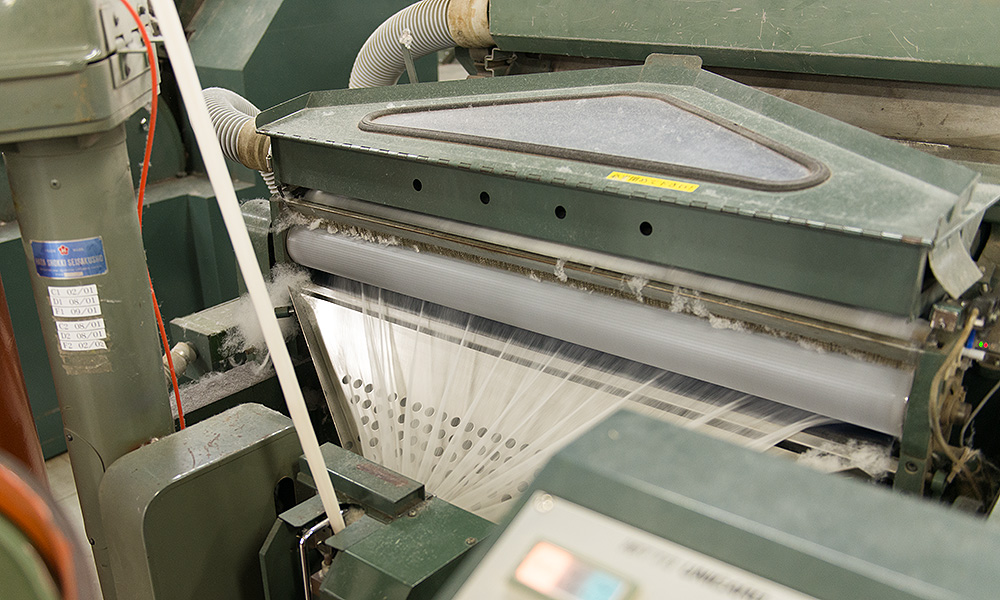 |
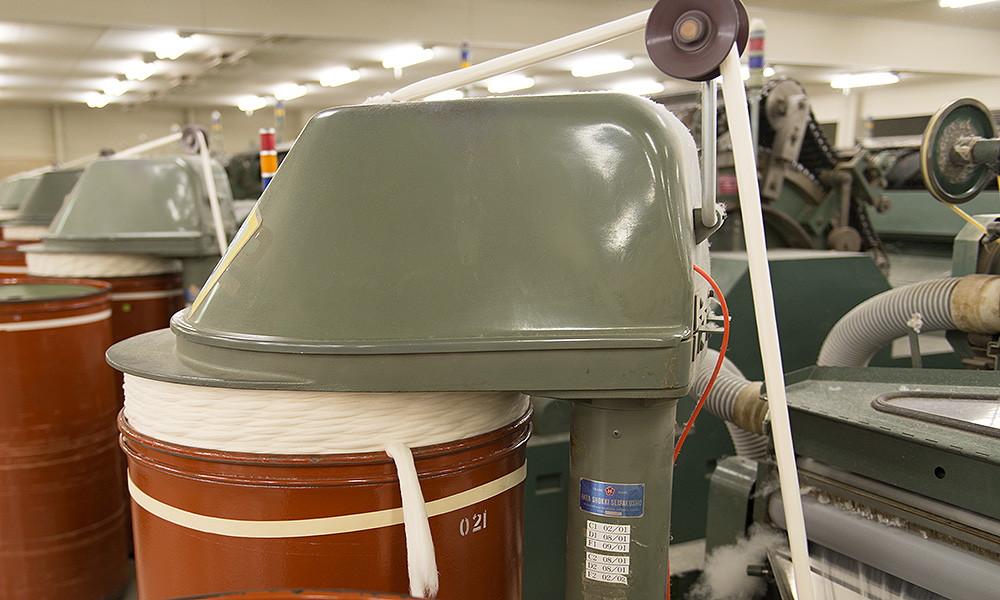 |
ロール状にまとめられた綿は「梳綿(カード)」という繊維方向を揃える工程に入る。櫛を使い一定方向に成った繊維がシート状になり、最後は撚りのかかっていないロープ状の「スライバー」になる。さらに、後の工程へ動かしやすい下にローラーがついたドラム缶のようなケースに収納されていく。 |
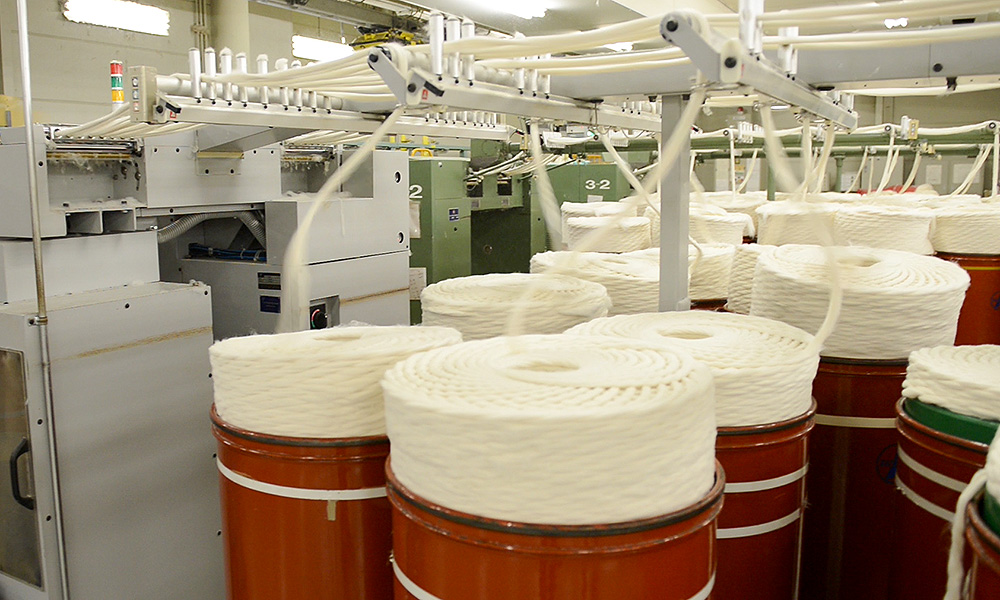 |
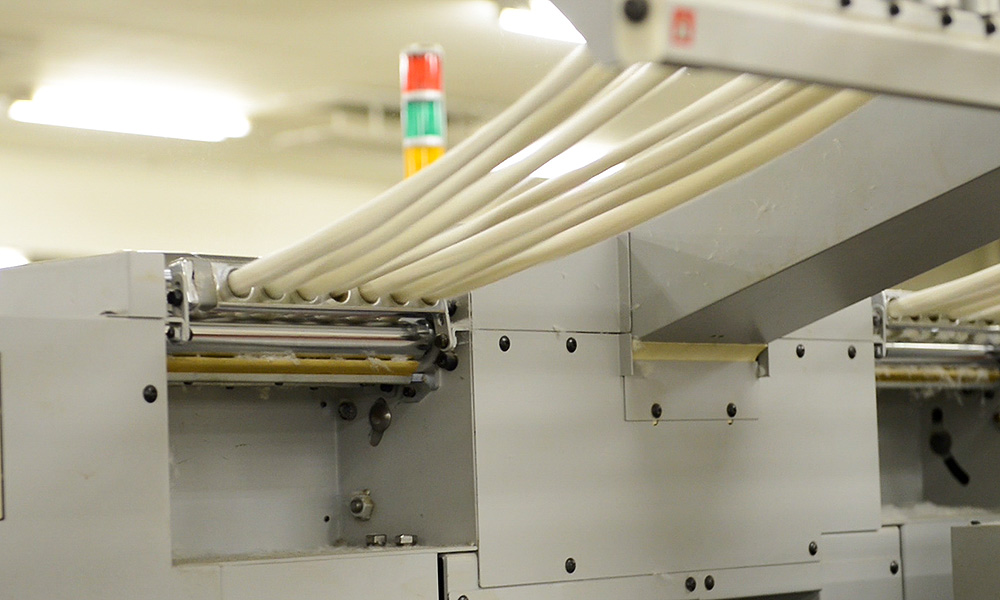 |
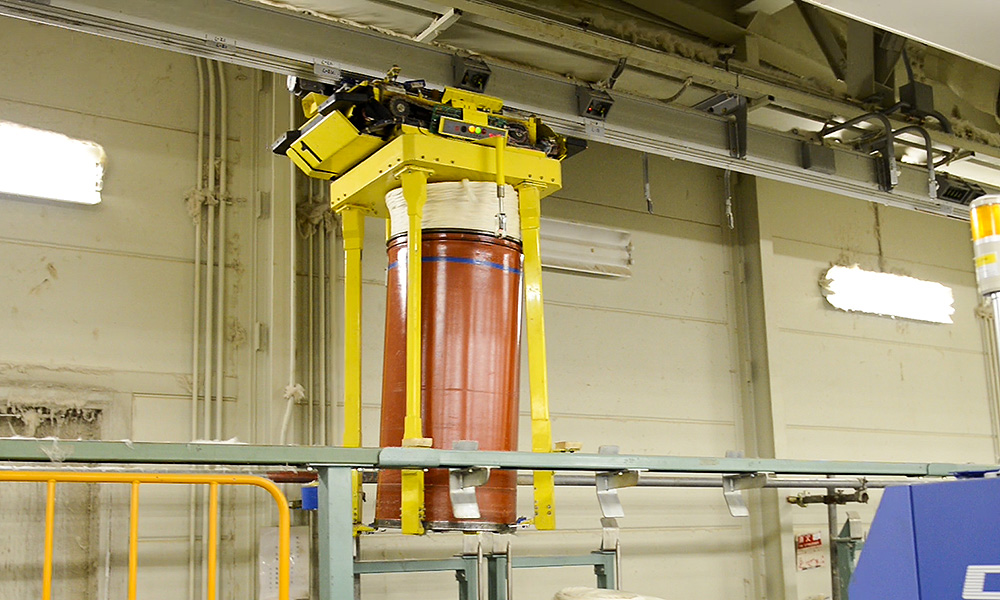 |
スライバーを縒り合せる練条。山忠紡績では7束のスライバーを一つに、さらに8束を一つに。結果、7×8=56本のスライバーを1本にまとめ、繊維の短い・長い/太い・細い部分を均整化する。できる限り均一な繊維の束を作る工程。 |